Enhancing an FDA centrifugal blood pump through simulation and parametric design optimization
Written by Braydan Collins, Claudio Miccoli and Angela Scardigli
28 March 2024 · 5 min read
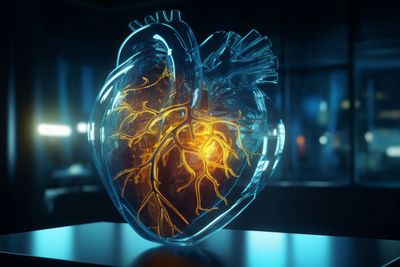
The rise in cardiovascular diseases combined with the limited availability of donors for heart transplantation has led to extensive efforts towards developing ventricular assist devices (VADs) to treat heart conditions. In most cases, these pumps assist the heart ventricle in pumping blood to the patient's body. However, device reliability and mechanical blood damage still pose serious challenges in clinical applications, limiting their potential. This is one of the reasons computational fluid dynamics (CFD) has become a fundamental technique for designing and predicting cardiovascular device performance. The U.S. Food And Drug Administration (FDA) blood pump design is a crucial development in this field. It serves as a benchmark for testing and validating CFD models used in the design of these medical devices.
We developed a comprehensive numerical methodology to validate and optimize the high-fidelity simulation of a centrifugal blood pump, building on the FDA’s initiative to standardize and validate high-fidelity simulations for medical devices. In this study we demonstrated that our design optimization approach can easily be adapted to more complex VAD geometries. In this way, biocompatible and robust blood pumps can be designed, minimizing the risk of postoperative complications for patients.
CFD-based design optimization methodology for a centrifugal blood pump
To optimize the design of the FDA blood pump, we integrated multiphysics simulation with a modeFRONTIER workflow and employed a comprehensive exploration strategy that includes Design of Experiments (DOE), Response Surface Models (RSM) and multistrategy algorithms for robust shape design optimization. Our goal was to ensure that the blood pump design met the stringent requirements necessary for clinical application. In particular we focused on evaluating two critical factors:
- Hydraulic efficiency
- Hemolysis risk associated with elevated shear stresses, critical factors influencing blood damage
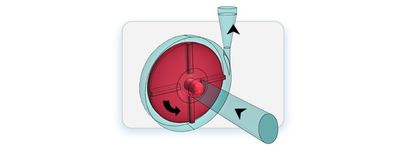
FDA blood pump baseline prototype
1. CFD simulation: modeling the FDA blood pump
The simulation of the FDA blood pump entails integrating various components and methodologies with a comprehensive computational model to ensure accuracy and reliability. Using the CFD software OpenFOAM, the simulation captured intricate details of the blood pump geometry through advanced meshing techniques. The Navier-Stokes equations governing fluid flow were numerically solved using finite volume discretization methods, enabling precise prediction of flow behavior within the pump. To accurately simulate the rotating components of the pump, we took a Moving Reference Frame (MRF) approach, facilitating efficient simulation of impeller rotation. Turbulence modeling, such as the standard k-Epsilon turbulence model, accurately captured turbulent flow phenomena, ensuring fidelity in predictions.
Validation of the CFD model
2. Hemolysis Modeling: Eulerian Approach
A paramount concern in blood pump design is minimizing hemolysis: the destruction of red blood cells due to excessive shear stress. To minimize hemolysis we employed a Eulerian approach, incorporating sophisticated techniques to accurately predict blood damage. Hemolysis is modeled using a passive scalar transport equation, simulating the transport of a scalar quantity indicative of blood damage. The von Mises stress field, correlated with the flow-induced stress, served as a key parameter in quantifying the risk of hemolysis, aligning with established empirical relationships.
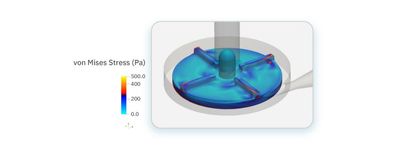
Von Mises stress field on impeller
3. Process automation and design optimization of a FDA blood pump with modeFRONTIER
Improving blood pump design requires a multi-objective optimization approach where both hydraulic efficiency and blood hemolysis levels are optimized simultaneously. We leveraged modeFRONTIER, a comprehensive process automation and design optimization software, to obtain optimal pump designs while navigating the trade-off between conflicting objectives. To streamline the optimization process, we used a workflow to automate multiple simulation tools. The geometry was generated in Siemens NX, identifying several notable features for potential improvement. ANSA (from BETA CAE Systems) generated a consistent and efficient mesh for the geometry. The meshed geometry then underwent analysis using the OpenFOAM CFD model to extract the necessary metrics for each objective.
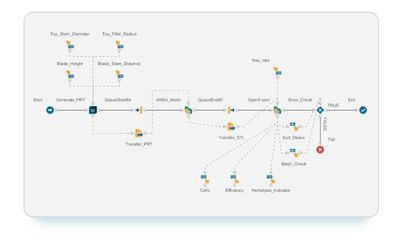
modeFRONTIER workflow for design optimization of the FDA blood pump
In a typical design process, engineers might need to repeat this process manually numerous times to obtain the required results. With modeFRONTIER, you can automate design optimization, automatically adjusting parameters in the geometry and analyzing the modified geometry without the need for manual input.
In our pursuit of optimizing the FDA blood pump for enhanced performance and reliability, we delved into the realm of Design of Experiments (DOE), a systematic approach essential for comprehensively exploring the design space. Central to our DOE methodology are four key geometric parameters governing the shape of the impeller:
- Blade Stem Distance (P1): This parameter controls the distance between the blades and the hub, influencing the flow dynamics within the pump.
- Blade Height (P2): Determining the height of the impeller blades, this parameter plays a crucial role in dictating fluid flow characteristics.
- Stem Diameter (P3): The diameter of the impeller stem affects the distribution of forces within the pump, impacting both efficiency and hemolysis.
- Top Fillet Radius (P4): This parameter controls the curvature at the top of the impeller blades, influencing fluid flow patterns and shear stress distributions.
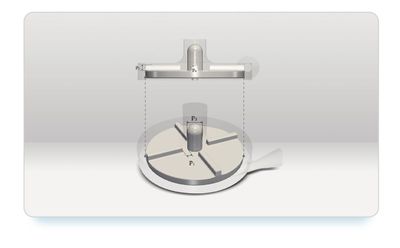
Geometric parameters on impeller
The effect of the four design parameters was sampled by generating a Design of Experiments (DOE) with 60 different potential designs. To ensure the best sampling techniques, we employed three algorithms: Uniform Latin hypercube to ensure a uniform distribution of designs, Latin Hypercube Monte Carlo to concentrate design points near the extreme values of each parameter, and Incremental Space Filler to fill any large gaps in the design space. Using the resultant DOE, we trained Response Surface Models (RSMs) to gain insight into the relationship between design parameters and critical performance metrics in a fraction of time. An RSM is a mathematical model used to predict additional design points based on existing designs, in a tiny fraction of time. Six different RSM algorithms were trained on the DOE data, with the Gaussian Process method emerging as the preferred choice due to its superior predictive accuracy. The trained RSMs were instrumental in guiding our optimization efforts, enabling the exploration of a vast design space with efficiency and precision. The ESTECO proprietary pilOPT algorithm facilitated the generation of 5000 design points forming a saturated Pareto frontier. To validate the RSM predictions, we performed an additional layer of validation on a few selected points from around the Pareto frontier. This validation step was crucial for verifying the performance of optimized designs under real-world conditions. The selected designs can be viewed below:
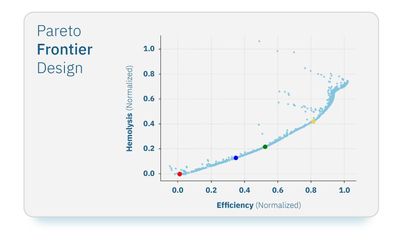
Pareto frontier designs: selected designs highlighted
In real-world blood pumps, the fluid flow rate doesn’t enter at a constant velocity, and is subject to some variation. This necessitates analysis under different fluid conditions at the pump inlet, to ensure the pump performance doesn’t drop off under different inlet conditions. To analyze other conditions, we imposed ‘stochasticity’, or a slight variation, on the selected designs. We then analyzed the performance of the pump under these varying inlet conditions to ensure the “robustness” of the pump. This robustness analysis provided insights into the stability of pump performance and its resilience to external factors. We analyzed the 4 selected optimized designs for their robustness characteristics. For each design, we sampled 10 different fluid velocity points. The ‘best’ designs are those which have a close grouping of points, meaning they will not experience large decreases in performance from small changes in inlet velocity.
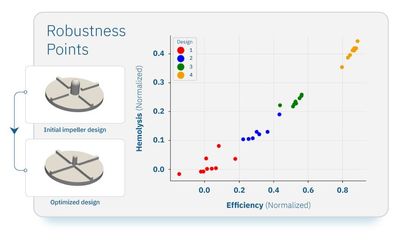
Robust design analysis results
Our DOE methodology, integrated with optimization techniques and robustness analysis, has opened up promising avenues for the optimization of the FDA blood pump. Through a systematic exploration of the design space and rigorous validation of optimized designs, we aim to drive advancements in blood pump technology, ultimately improving patient outcomes and enhancing the quality of cardiovascular care.
4. Employing Reduced Order Models (ROM) for quicker evalution of blood pump design configurations
The next step of our project is to employ Reduced Order Models (ROM), a mathematical technique that simplifies complex CFD simulations without significantly compromising the accuracy of the results. Our ROM Technology will be particularly valuable in the iterative process of blood pump design, where numerous simulations are required to explore the design space and optimize the device's performance. A limited series of CFD simulations of the blood pump will be the foundation for developing the ROM by combining techniques such as Proper Orthogonal Decomposition (POD) with Machine Learning (ML). We intend to extract the essential velocity field inside the pump through ROM, significantly reducing computational complexity. By abstracting the essential dynamics of the full-scale CFD model, ROM will facilitate quicker iterations and evaluations of various blood pump design configurations.
modeFRONTIER is the leading software solution for simulation process automation and design optimization
Design better products faster
modeFRONTIER is the leading software solution for simulation process automation and design optimization
Design better products faster
modeFRONTIER is the leading software solution for simulation process automation and design optimization